The Plastic Pipe Manufacturing Process: An Overview
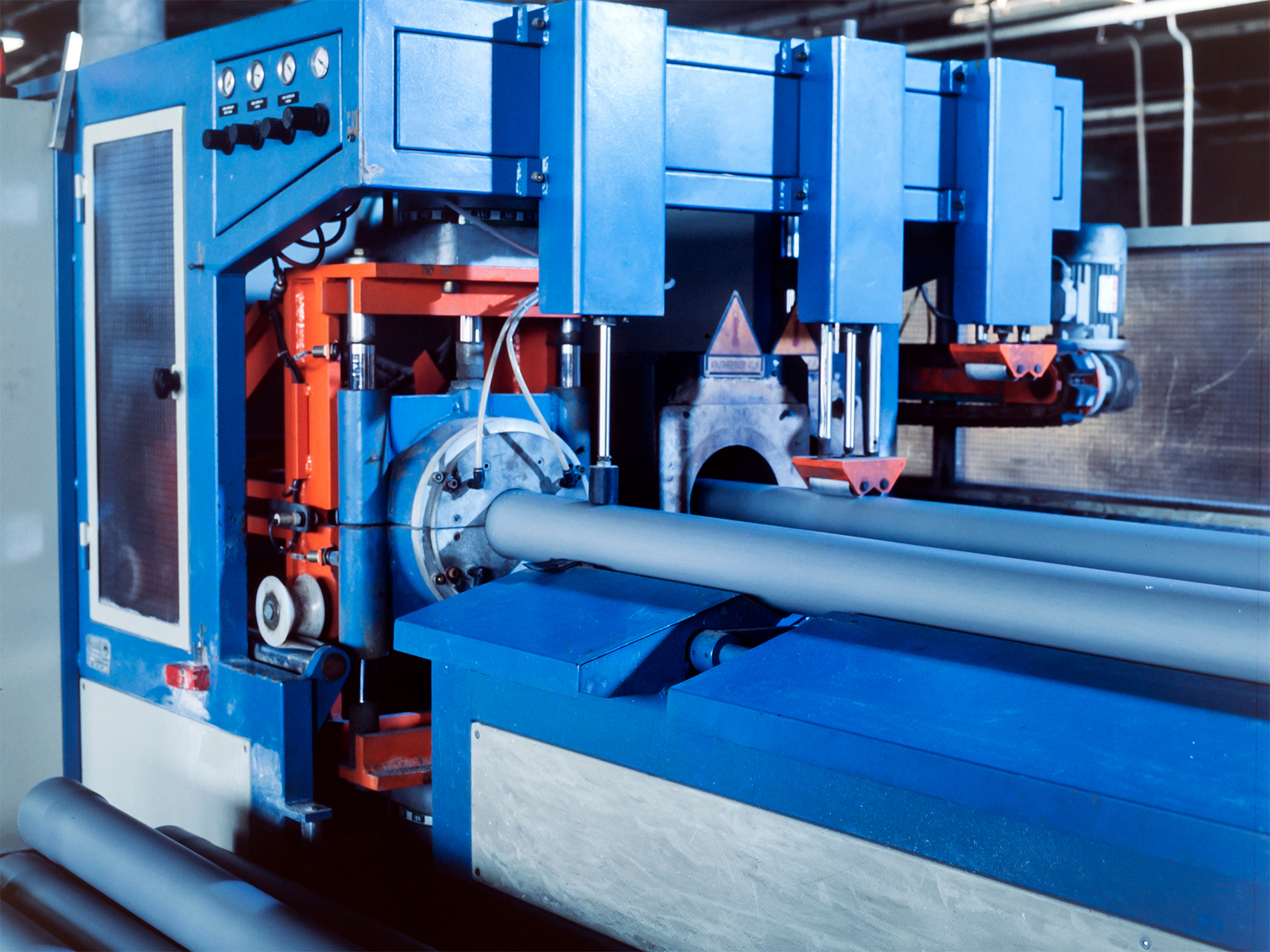
The polyvinyl chloride (PVC) market is projected to grow at a compound annual growth rate (CAGR) of 5.79% from 2021 to 2030 and be worth $87.15 billion by the end of the forecast period. Likewise, the high-density polyethylene (HDPE) market, at a CAGR of 4.65% from 2022 until 2027, is expected to be worth $97.4 billion by 2027.
Indeed, the plastic pipes market is growing and will continue to expand. You can expect more homeowners and contractors opting to use HDPE or PVC duct pipes where once they would’ve considered utilizing only galvanized steel.
The reason: Plastic pipes are durable, strong, flexible, and resistant to corrosion, abrasion, and biological growth. They’re not perfect, but they are virtually indestructible when used according to specifications and installed correctly.
Let’s explore how PVC pipe is made.
How PVC Pipe Made
The following are two commonly used pipe manufacturing processes.
Extrusion
Extrusion refers to forcing or pushing material through and out of a die that will form it into the manufacturer’s desired shape and size. This process is a standard method for producing PVC and HDPE pipes.
In the plastic pipe extrusion process, the manufacturer loads the raw material (the PVC or HDPE in powder or pellet form) into a hopper, which gradually feeds it into the barrel of a single or twin-screw extruder.
Inside the barrel, the raw material is heated to approximately 200°C. This causes the powder or pellets to melt. The extruder then pushes the melted plastic through an annular die, thus creating a continuous plastic tube or cylinder.
This continuous tubular plastic melt then goes through a vacuum or pressure calibration. In the vacuum sizing box, the vacuum on the outside of the pipe expands the still malleable plastic tube to its actual production size.
Next, the continuous plastic tubing is cooled, either by spraying it with water as it emerges from the calibration tank or by pulling it in and through a water immersion chamber.
The water-cooled pipe is then extracted from the extruder and into the cutting unit, where it is cut into the required length, after which the cut pipe is socketed, belled, or coiled according to production requirements.
Note: The above is the general extrusion process followed when manufacturing single-wall, homogenous pipe variants. A modified extrusion process is followed when manufacturing other plastic pipes (e.g., corrugated pipes, multi-layer co-extruded pipes).
Rotational Molding
Rotational molding is typically used to make large, single-piece products.
In this alternative manufacturing process, the raw material (i.e., plastic powder) is fed into a mold that continuously rotates inside a furnace. The rotating motion of the mold throws the powder against the mold’s hot inner surface and melts it, which forces the melted plastic to take on the mold’s shape.
Rotational molding is a relatively straightforward process as the plastic is melted and shaped inside the mold. The mold, therefore, yields a complete, one-piece plastic product.
However, rotational molding is also less flexible and versatile than the process of injection molding. A rotational molding machine typically has a fixed mold that cannot be exchanged for another.
How Plastic Pipe Fittings Are Made
The following are two commonly used methods for manufacturing plastic pipe fittings (e.g., HDPE and PVC pipe fittings).
Injection Molding
In injection molding, the manufacturer puts the raw materials (e.g., plastic powder) into a hopper that feeds it to the injection molding machine. The injection molding machine, like the extruder machine, heats the plastic until it melts.
This is where the similarity between extrusion and injection molding ends. In extrusion, the melted plastic is pulled through a die-head to create a continuous tube melt, which is processed as described earlier. In injection molding, the melted plastic is homogenized and poured into the molds.
Next, the molds are cooled. Once the melted plastic inside has cooled down, the molds are opened, and the molded plastic fittings are ejected.
In injection molding, the mold gives the melted plastic its final shape and dimension. To make a T-piece, for instance, the manufacturer has to pour the melted plastic into a T-piece mold that’s in the size and shape desired of the finished product.
Fabrication
In fabrication, the pipe manufacturing facility creates plastic pipe fittings and accessories in the context of the specific piping system application. In other words, plastic pipe components are made according to custom specifications, or small fittings are tailored on demand to repair pipes or fulfill specific requirements.
Plastic pipe fabrication offers the most versatility and flexibility among pipe manufacturing processes. When fabricated, plastic pipes, pipe fittings, and pipe accessories can take on complex shapes. However, fabrication is also more labor-intensive than other manufacturing processes.
Manufacturing Plastic Pipes and Fittings
Extrusion is a common plastic pipe manufacturing method. However, rotational molding may be a more practical approach when making one-piece plastic products like inspection chambers. Meanwhile, injection molding is the mainstream process of manufacturing pipe fittings unless custom specifications demand fabricated fittings instead.
Polyfab Industry is a plastic piping solutions provider in the United Arab Emirates.
We manufacture plastic pipes, pipe fittings and accessories, and we provide equipment and technical support to our construction and infrastructure industry clients in the region.
Contact us to learn about our plastic pipe solutions.
We're here to help
Let our specialists help you find the right piping products for your needs. Get access to expert services and top-of-the-line supplies for quality, on-time, professionally delivered projects. Get in touch with the Polyfab team today.