A Look Into the Different HDPE Pipe Fusion Methods
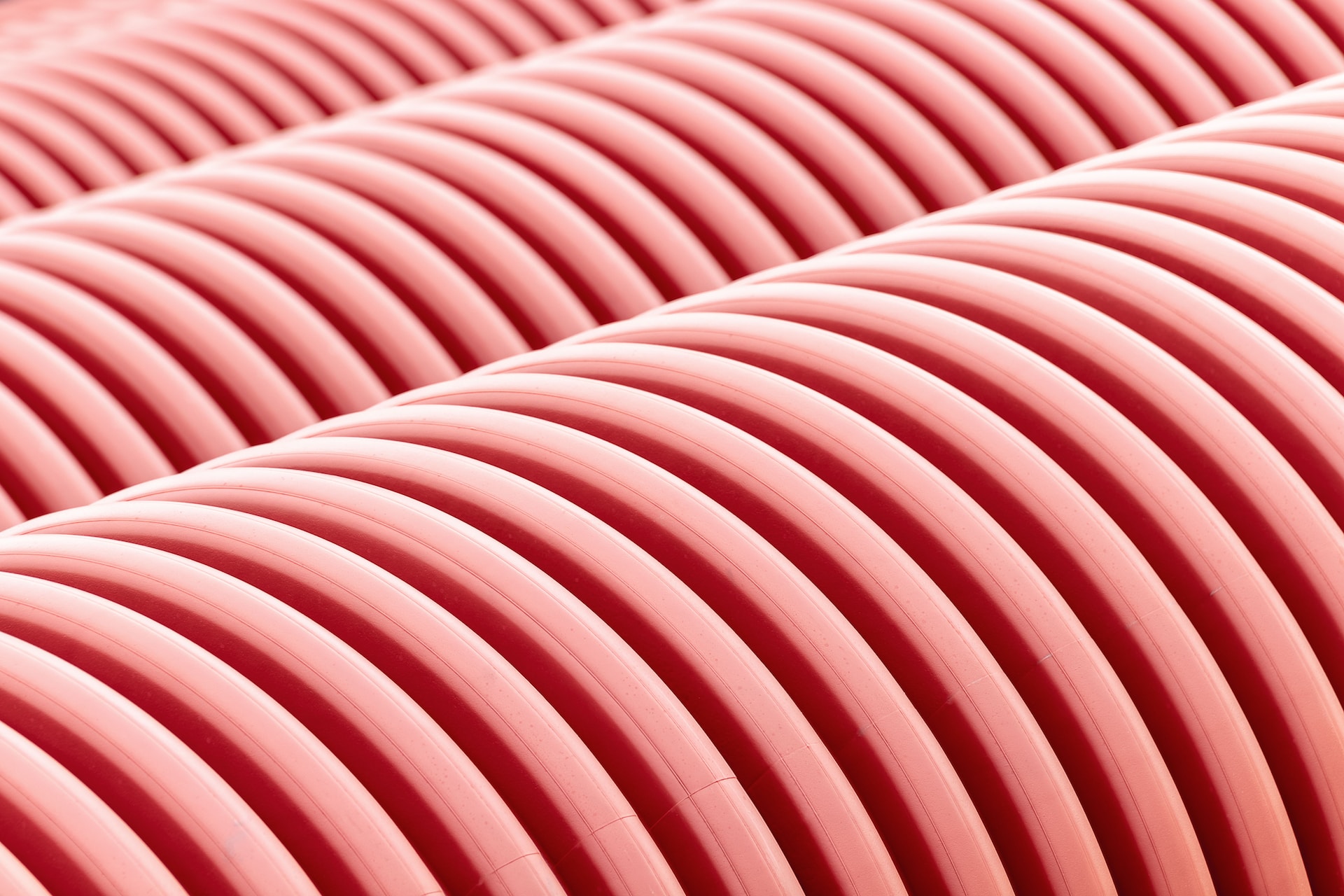
High-density polyethylene pipes can come in different lengths. Straight lengths of HDPE pipes for water supply and other high-pressure applications typically range between 20 and 100 feet.
If you need a longer length of pipe, you can use one of the primary HDPE pipe fusion methods that join pipes together using heat.
How are HDPE pipes most commonly joined? Learn about the main HDPE pipe fusion techniques contractors use to join HDPE pipes in this post.
Butt Fusion
Butt fusion is a heat fusion process that joins two lengths of HDPE pipes together using a butt fusion machine. Butt fusion gets its name because the process involves fusing the butt ends of two HDPE pipes.
Butt fusion is an ideal pipe fusion technique if you’re joining two pipes with identical diameters and wall thicknesses. When joining two HDPE pipes with the same size but different wall thicknesses, consult an HDPE pipe fusion expert, preferably from the pipe manufacturer.
The Butt Fusion Process
Butt fusion involves these steps:
- Use a paper towel to clean and clear off any dust and debris from the pipe ends.
- Fix the HDPE pipes in place in a butt fusion machine. Make sure they’re perfectly aligned.
- Let the facing tool attachment trim the butt ends and give them clean and parallel, fusion-ready surfaces. Do not touch the prepared ends of the pipe after facing to prevent contamination that can lead to an imperfect fusion.
- Check if the pipe ends remain perfectly aligned. If not, realign the pipes and repeat the facing or trimming procedure.
- Once the pipe butt ends are ready and the pipes are perfectly aligned, prepare the heating plate on your HDPE pipe fusion machine. Make sure it has been heated to the correct temperature, usually between 400 and 450°F.
- Next, mount the heating plate between the two pipes, gently place the pipe ends against the plate, and let the heat soak in for an appropriate amount of time. The pipe diameter and thickness will dictate how much heating time the pipes require.
- Once the heating time is over, remove the heating plate and inspect the butt ends to see if they have completely, properly and smoothly melted. If they are, forcefully join the pipe ends together and leave them clamped in place, undisturbed, until the prescribed cooling period has passed.
Computer Numerical Control (CNC) Butt Fusion Machine
If your project requires extreme precision, use a CNC butt fusion machine to butt-fuse HDPE pipes. A CNC butt fusion machine is computer-aided and guided to ensure precise facing preparation and exact alignment.
We are one of the pipe installation companies in the UAE that provide CNC butt fusion machine sales and rental. We also provide expert and precise HDPE butt fusion and installation services.
Electrofusion
Electrofusion is a heat fusion technique that joins two pipes indirectly through a special HDPE pipe fitting. HDPE pipe fittings used in HDPE electrofusion have an embedded heating coil or resistive wire that may be activated using an electrofusion machine.
Electrofusion, like butt-fusion, requires specialized heat fusion expertise.
Your fitting will vary according to the pipe’s standard dimension ratio, i.e., the ratio of the pipe’s thickness to its outside diameter. If you use an inappropriately heavy-duty pipe fitting on a thin HDPE pipe, the pipe can collapse or melt. You can also cause a fire. In any of these scenarios, you will get a subpar joint.
The Electrofusion Process
Electrofusion entails following these steps:
1. Use a pipe scraper to remove approximately 0.0118 in of surface oxidation layer on the pipe ends. Refer to the HDPE pipe fitting specifications to know how wide of an area you must scrape off the pipes to be jointed.
2. Remove any dust and debris from scraping by wiping the area with an isopropyl alcohol pipe wipe. Let the surface dry completely.
3. Slide the pipes into the fitting, one on each end.
- The inside of the fitting and the exterior wall of the pipes are flush together.
- The pipes being joined through the fitting are aligned and free from bending stress.
- The pipes are securely clamped in place so they cannot move.
- There’s no wind blowing in through the pipes, which can cool the fusion zone.
4. Use the electrofusion machine to activate the heating coil embedded in the fitting. Follow the machine’s instructions and the guidance from the fitting manufacturer to know how much heat soak time is required.
5. After electrofusion, let the assembly cool for the prescribed time, then let the fused pipes rest (do not subject to pressure) for a separate period.
Socket Fusion
Socket fusion heat-fuses a pipe to a socket fitting. This process works best for smaller-diameter pipes that must change direction.
The Socket Fusion Process
The procedure is the same as butt fusion. However, the HDPE fusion machine has a heating adaptor that simultaneously heats the outside of the pipe and the interior of the socket.
Once the exterior of the pipe and the interior of the socket are correctly melted, the pipe is pushed into the socket and allowed to cool (under pressure) and rest.
Saddle Fusion
The saddle fusion is heat-fusing a saddle fitting to a pipe. Use saddle fusion to create a leak-free joint between a new branch and an existing line.
The Saddle Fusion Process
Saddle fusion involves the following steps:
- Clean the surface of the saddle fitting and the exterior of the existing pipeline.
- Position the saddle fitting on the area where it will be joined to the pipe.
- Use the heating adaptor on the HDPE fusion machine to simultaneously heat the concave surface of the saddle fitting and the corresponding surface on the pipe exterior.
- After the heat soak, push the fitting against the pipe to create the heat-fused joint.
- Let the joint cool (under pressure) and rest.
Once the prescribed cooling and resting time has passed, you can use a hot tap tool, inserted through the saddle fitting, to drill a hole into the existing pipeline. This will create a new service line or branch from the existing line.
What Is the Best Way to Connect HDPE Pipes?
Heat or thermal fusion is the best way to join HDPE pipes. It effectively creates permanent, leak-free, homogenous, and self-restraining joints.
There are four HDPE pipe fusion methods: butt fusion, electrofusion, socket fusion and saddle fusion. Use butt fusion to fuse together pipe ends, electrofusion to join pipes with an electrofusion pipe fitting, socket fusion to connect small-diameter pipes with socket pipes, and saddle fusion to tap into an existing pipeline.
For expert advice on pipe fusion, contact Polyfab Plastic Industry LLC. As a leader in plastic pipe manufacturing in the UAE, we manufacture HDPE pipes and pipe fittings for turnkey HDPE piping solutions, rent out and sell HDPE fusion machines, and provide expert HDPE pipe fusion and installation services.
We're here to help
Let our specialists help you find the right piping products for your needs. Get access to expert services and top-of-the-line supplies for quality, on-time, professionally delivered projects. Get in touch with the Polyfab team today.